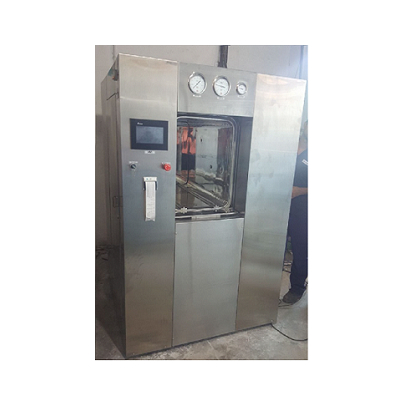
Salient Features
Single door Steam Sterilizer, Sliding Door, Rectangular chamber Scope of Supply:-
1) Basic Unit
2) S. S Carriage 1no.
3) S. S Floor Trolley 2 nos.
4) Automation -
Fully Automatic and 3 level password protected PLC based control system Including Pneumatic actuated Valves, Solenoid
Valves, Pressure Transmitter, S.S control Panel etc
5) Vacuum Pump ( Water ring type ) with S.S condenser Installation and commissioning charges
SALIENT FEATURES OF ESTEEM AUTOCLAVE
Autoclave will be in sturdy construction using plates of appropriate thickness which prevents buckling under vacuum or bulging due to pressure. Made to confirm to EN 285 or HTM 2010 performance requirements.
Fully automatic by means of PLC based controls, which operate pneumatically actuated solenoid valves. Provision of four different cycles and programs : Autoclave will be provided with an air filter of 0.2 microns (PTFE Membrane Capsule Filter type) for breaking the vacuum.
Suitable for standard and custom sterilisation cycles at 134 °C and 121 °C, with pre-vacuum, conditioning/sterilisation and post-vacuum/drying phases.
The technique uses the method of gravity air removal to ensure uniform steam distribution and penetration.
Steam trap equipped with air vent ensure maximum air removal.
Useful for sterilization of glass containers i.e. ampoules, vials, glass bottles etc.
It is also useful for Sterilization of glass wares, utensils, vessels, instruments, rubber articles linen etc. in Laboratories and hospital.
HP HV cycle
2a. 3 pre ster vacuum pulses – heat up – ster hold – exhaust
2b. 3 pre ster vacuum pulses – heat up – ster hold – exhaust – post ster vacuum pulsing for drying
Preset cycles, including at least for instruments (134 °C), textiles (134 °C), mixed load (121 °C and/or 134 °C), heavy load (134°C), prions (134 °C) plastic/rubber (121 °C), liquids (121 °C and/or 134 °C), glassware (121 °C and/or 134 °C), fast cycle (134 °C), Bowie-Dick test, vacuum and self test.
This technique uses near 100% air removal from sterilization chamber which results in better temperature uniformity in the chamber because of the absence of air pockets i.e. cold spots.
This technique increases the penetration of steam in porous products from which removal of air is difficult.
Vacuum drying at the end of sterilization hold period ensures drying of the material which has been sterilized.
This cycle is useful for garments, fabrics, drying rubber bungs vessels machine parts etc.
. Leak Test Cycle for periodic testing of door integrity and pipeline connections & detecting leakage ampoules.
. Another HP HV cycle with post vacuum pulses can be provided, if required, for special purpose.
III General Information –
itch which shuts off steam supply to the chamber.
Type : Rectangular
M O C contact parts : S S 316 L 6 MM
Factory tested at working pressure >2.3 bar
6. OPERATING PARAMETERS :
Temperature : 134°C Max.
Pressure : 2.31 kg / cm2. Max.
Vacuum : Full
8. MAINTENANCE AND CALIBRATION
SCOPE OF SUPPLY FOR STEAM STERILIZER
1. Interconnecting piping |
|
|
M O C : S S 316 : |
1 Set |
|
2. Pneumatically actuated Valve : |
1 Set |
|
3. Poppet / Solenoid Valve |
: |
1 Set |
4. Spring loaded safety valves: 3 Nos. |
|
|
5. Steam traps for condensate |
|
|
Evacuation from jacket & chamber |
: |
2 Nos. |
6. S S port for insertion of multiple |
|
|
Probes for validation |
: |
1 No. |
7. Pressure and compound gauges |
: |
3 Nos. |
8. PT – 100 (RTD) probe at drain (Duplex) |
: |
1 No. |
9. Temperature dial gauge |
: |
1 No. |
10. S.S 304 mounting stand |
: |
1 No. |
11. Air Vent Filter : |
1 No. |
|
12. Pressure / Vacuum switch |
: |
1 set. |
13. S.S control panel 14. Trolley & Carriage 15. Loading Trays |
: : : |
1 No. 2 nos. 2 Nos |
UTILITIES REQUIRED AT BUYER’S FACILITY FOR FUNCTIONING OF THE STEAM STERILIZER
Steam : Dry saturated steam at 3 kg/cm2
Through your P.R.V
Air : Compressed air through F R L will be
Required at a pressure of 6 kg/cm2 for operating pneumatic valves and door.
Vacuum : Full / as required tube type condenser for Vacuum Pump.
Water : Inbuilt Water for water ring vacuum pump
with 27 m3/hr capacity for negative pulsing & drying.
Power supply : Single Phase, 230 Volts. Three Phase, 440 Volts
Size : 600 x 600 x 900
600 x 900 x 1200
900 x 900 x 1200
600 x 600 x 1500
Product Code:ESTA -108 A